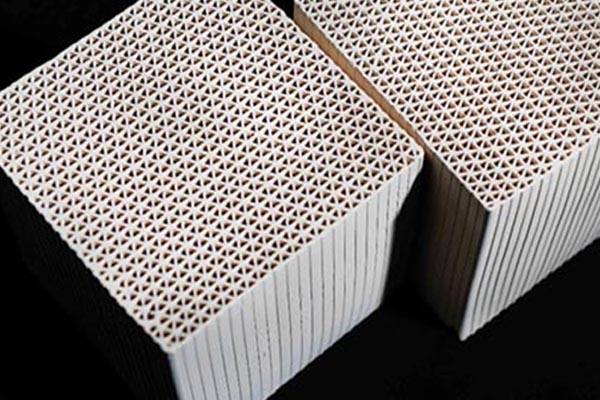
The molecular sieve adsorption runner system uses the continuous process of adsorption desorption concentration incineration to treat and purify VOCs waste gas, which has the advantages of wide application range, high safety and stable operation. However, in different practical applications, the composition of exhaust gas is complex, and the residual polymerization of VOCs with high boiling point and smouldering phenomenon are easy to occur
1. High boiling point VOCs residual polymerization
When the waste gas contains VOCs with high boiling points, if the desorption heat is insufficient and the adsorbate is not completely desorbed, the adsorbate will accumulate and remain in the near adsorption period, and polymerization will occur over time, which will block the adsorption position of zeolite, resulting in reduced adsorption efficiency in this area. In order to completely desorb the high boiling point VOCs adsorbed in zeolite, the following suggestions are given:
(1) Set the front-end VOCs removal equipment with high boiling point
In order to avoid the difficulty of desorption caused by the adsorption of VOCs with high boiling points, a pre filter cloth or Activated carbon Filter, install demister or condenser, and remove VOCs with high boiling point first.
(2) Increase desorption heat capacity
Method 1: In order to increase the desorption temperature, it is suggested that the temperature should be controlled between 180-200 ℃, not more than 220 ℃, so as to avoid incomplete cooling caused by excessive waste heat and affect the effect of the adsorption section; The other method is to increase the desorption regeneration air volume and reduce the concentration multiple, so as to achieve full desorption regeneration effect.
(3) Regular maintenance and cleaning with clean water
Attention shall be paid to the water quality during cleaning. If there is a large amount of calcium and magnesium plasma in it, carbonate may form in the zeolite, blocking the honeycomb pores of the zeolite runner; The chloroform in the water may occupy the adsorption position of the zeolite, hindering the adsorption efficiency of VOCs. In addition, the trace heavy metals contained in the water will also poison the zeolite. Therefore, it is recommended to use high-pressure nozzle to form fine droplets of cleaning water, and use clean air in the cooling section of the system as the air carrier.
(4) Conduct high-temperature desorption regeneration regularly
Regular high-temperature desorption treatment will effectively remove the high boiling point VOCs and activate the zeolite runner. Generally, 300 ℃ is the appropriate desorption temperature.
2. Smoldering occurs
Under the condition of desorption at 180-200 ℃, if the system abnormally stops without airflow and external oxygen supply, the VOCs composition in the exhaust gas and the high boiling point substances polymerized on the runner will take advantage of the catalytic reaction between the zeolite in the runner and the oxygen originally left in the runner channel and the zeolite pore to form exothermic combustion and destroy the zeolite structure. In order to prevent the occurrence of smoldering, it is recommended to use pure gas (such as nitrogen) as the protective gas when the system is shut down abnormally, and at the same time use water spray device as the solution to prevent the smoldering phenomenon from continuing.